Unit 4 - Project
Unit 4 - Project
Level Design:
Show elements (e.g: landscape, vehicles, sky)
Can be done through video, qt, snipping tool.
HOW?
Creative Portfolio.
Crisis Management:
7 steps:
1. Have a plan B in case of absence of myself or my team members and/or me being behind on work. What are the objectives? Assistant Producer. Who/what is affected (regarding the project)?
2. Spokesperson. One voice. Mantra. Purpose. Consistent message.
3. Honest and open with colleagues and the client.
4. Inform the whole team. Business as usual.
5. Client informed. Email. Invite (if required).
6. Update the team often to avoid rumours.
7. Social Media. Behaviour is different. Talk about how you communicate each day.
My Crisis Plan:
1. I am in charge of making the 3D models for the project by using Maya 2019. However, since I have Maya 2019 at home as well as Discord, it will not matter as much if I am absent since I will still be able to work on the models and network with my fellow teammates from home.
2. As the group leader, Jordan Page will be our spokesperson.
3. I must make sure to be honest and own up to any issues or mistakes I end up running into so that my teammates can figure something out.
4. I must make sure that I inform the team about any problems that could affect the project as a whole.
5. We must keep our client Karen updated regularly through emails or by inviting her to showcases in order to make sure she still has trust and confidence in us.
6. The same should also apply to keeping each other up to date on our progress so that we can maintain a steady pace and order while working on the project.
7. To maintain communication outside of college, we shall be networking through our Discord server and occasionally sharing our progress.
Meeting (Team):
Agenda
Chairperson
Video recording/photos
Meeting (Team):
Agenda
Chairperson
Video recording/photos
- Date and Day
- Participants (& regrets)?
- Corrections of previous meeting
- Agenda Items (1, 2, 3 and so on...)
Actions to be taken
Purpose and person
One person shows an idea and two people second it.
Majority vote
New business? AOB (Any Other Business)
Next meeting agreed weekly.
TRELLO
Team crisis management/contingency plan:
If a member of our team is absent, it will affect what can be completed and the stress of people gets increased because other people will take action over the work that the other members need to get completed. Jordan Page, the group leader, will be taking over anything that needs to be done that isn't currently being worked on between each role.
Harry Reader is our spokesperson, if he's unavailable then it's Jordan Page, then Bryant Haring, George Holt, then Harry Lewis.
Client is updated only if they need to be. When they come in they will be updated regardless if there's anything that we need their thoughts on or not.
In the event of the team having a crisis, details of the crisis itself are recorded on the team's Trello at https://trello.com/b/7xiGaeVs/team-2, and if the team doesn't check the Trello to see if there's a crisis then they are informed through other communication means e.g. text messages, calls, Discord direct messages, etc. The team will also be updated through these ways or other ways that they prefer to be contacted by.
29/4/20 Meeting:

In this meeting, we discussed what we've been working on and let each other know about our smart targets. We also decided on our agenda for the day (and to an extent, the days building up to May 6th.)
Members that participated:
George Holt
Bryant Haring
Harry Lewis
Harry Reader
Members that were absent:
Jordan Page
Agenda:
6/5/20 Meeting:

Meeting Participants:
Harry Lewis
Harry Reader
George Holt
Bryant Haring
--------------------------------------------------------------------------------------------------------------------------
Development Log
Keypad Model
24/3/20 (continuation of working on the keypad model):
Extruded the faces near the top of the keypad to start forming the anti-glare hood.
Dragged the vertices on the bottom edges of the hood and merged them with the surface vertices.
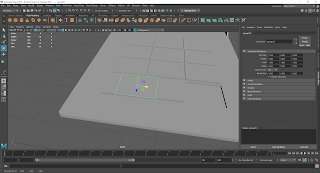
Duplicated the button mesh to place over the other gaps.
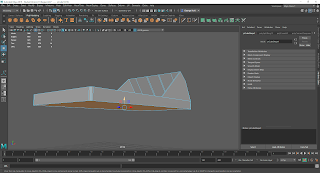
Dragged the bottom of the base downwards for extra thickness.
Cut singular edges in surfaces that wrap around completely in the UV editor.
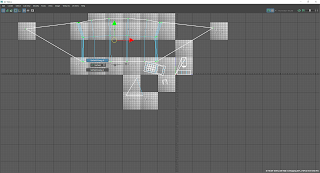
Unfolded each surface in the UV editor.
Shrunk the completed UVs into the first big square on the map for easier texture photoshopping.
Fully UV-mapped mesh.
The same UV-mapping process is done for each of the buttons.
The buttons are dragged back into place without being combined with the base mesh, and thus, ready for being animated.
Memory Chip Model
8/4/20 (modelling and UV-mapping the memory chip in its entirety):
A cube primitive is created.
The cube is then scaled up into a cuboid shape, forming the base of the chip.
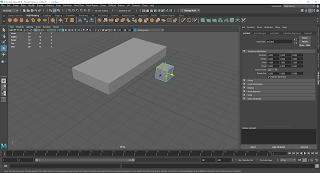
Another cube primitive is created.
The cube is then extruded.
Once extrusion is complete, the curves are bevelled in order to look smoother.
The mesh is then scaled appropriately, forming the prongs.
The edges of the base are bevelled.
The prong mesh is duplicated up to 32 times, so that 33 will be on either side.
The end of the base is dragged out to fit all 33 pairs of prongs.
Width of the base is also increased, but again, by dragging out one of the faces so that the first set of prongs stays in relatively the right place.
The prongs are mirrored in order to form the second set, which will be placed on the opposite side.
The two prong sets are then separated from each other for the time being.
A planar UV map is created for the faces on the base.
For any maps that loop around, a random edge on it is cut in order to ensure it unfolds properly.
The maps are then unfolded until they are neat enough so that distortion is reduced as much as possible.
The same process is then carried out for the UVs for the prongson the right...
... as well as the UVs for the prongs on the left, separately. Additionally, once the UV map for one of the prongs on one side are complete, the others on that side are deleted and replaced with new ones with the complete UVs via the aforementioned duplication process.
All the meshes are then combined with each other.
15/4/20 (finishing the memory chip UV):
After the meshes are combined, all the UVs in the combined object are then properly separated from each other, ready for texturing.
Control Panel Model
16/4/20 (starting on the control panel model):
Inserted a cube primitive.
Scaled up the cube into a more flat, rectangular shape to form the base of the panel.
Inserted edge loops all over the base for extrusion.
Extruded the faces that form the main screen frames.
Merged the vertices in the corners of the frame in order to make it more edged.
Used the connect tool to connect corner vertices and make the edges look more visible and polished.
Extruded the screen faces out a little bit to more easily separate them from the rest of the base.
Extruded the faces separating the three screens.
The vertices of the frame and the faces separating the screens are merged for additional clean-up.
More edge loops are inserted in order to extrude the faces representing the buttons.
The square faces on the base are extruded, forming the buttons.
The multi-cut tool is then used to create octagon-shaped faces in the base.
17/4/20 (continuing with the control panel):
Two of the vertices in each octagon face are properly connected once cutting is complete due to the cutting failing to register otherwise.
Excessive edges are then deleted and the octagon faces are extruded.
The front faces are then scaled down on all axes to form a more frustum-like shape and thus make them look more like dials.
Even more edge loops are inserted in order to create the faces that represent the sliders.
The faces representing the frame of the sliders are then extruded..
...followed by the faces representing the sliders themselves.
20/4/20 (finishing with the actual modelling process for the control panel):
Edge loops are inserted near the bottoms of the dials.
The new faces formed by this are then extruded to complete the dials by making them stick out from the base more.
22/4/20 (applying final cleanup and UV-mapping to the control panel):
Excessive vertices and edges are removed from the back of the base.
A planar UV is created for each surface on the mesh.
If the surface loops around, a random edge is cut in the UV editor in order to ensure the map is completely flat upon unfolding.
The map is then unfolded and all UV distortion on that respective surface is removed.
Additional edge/vertex cleanup is carried out on the slider frames.
Once all the surfaces on the control panel have been UV-mapped, they are then organised and grouped together and scaled down to fit into one big square on the graph. From there, the model is ready to be textured.
Ship Model (exterior)
6/5/20 (beginning work on the exterior of the ship model):
Inserted a sphere primitive.
Dragged out and scaled out parts of the circle in order to create a more spaceship-like shape.
Faces on the back of the mesh are deleted.
The hole is then filled back in with the fill tool...
Vertices on either side of the face are then joined together via the component connector tool in order to form new vertices, whilst still ensuring that the centre surface is flat.
The same face is then scaled and positioned to match the intended shape.
Vertices along the edge of the top surface are positioned in order to form a straight set of edges.
The top surface is then deleted and filled back in for flatness.
Excess vertices are then deleted as part of cleanup.
The mesh is then scaled up in order to match the intended proportions (so that it is in accordance to concept art).
11/5/20 (continuing with the ship exterior):
Circular edge loops are formed by vertices which are created with the multi-cut tool.
The circles formed from multi-cutting are then extruded.
The surfaces on the tops of the extruded circles are then deleted and re-filled.
These faces are then poked..
..and dragged out in order to make the surfaces look flatter and more organised when they are deleted again.
Once the surfaces are re-deleted, the edge loops on the ends of each cylinder are scaled outwards from each other in order to look more separated from each other.
Through the use of the edge loop insertion tool, edge loops are inserted on the front of the mesh.
The vertices on the top ends of both pairs of loops are joined together via the component connection tool.
The surfaces in between these inserted loops are then extruded inwards a little bit, thus forming the ship's windows.
With the windows extruded, the connections inserted earlier are deleted as part of clean-up.
More edge loops are inserted on the side of the mesh.
Gaps in the edge loops are then joined together via vertex connecting.
12/5/20-13/5/20 (finishing the ship exterior):
The edge loops on the insides of the cylinders on the back are extruded inwards..
..and the vertices on the end of each edge are merged together so that the holes are properly filled in.
The centre vertices of certain surfaces are dragged into the edges and vertex merged into them.
Sometimes, these centre vertices are chambered via the vertex chamber tool before being merged in order to properly close the holes.
Now that the holes are completely filled in, the thrusters of the ship are now fully formed.
The edge loop on the bottom end the base of the ship is extruded in order to ensure that the sides of the ship are at 90-degree angles.
The edges on the ship's side inserted from earlier are then re-positioned accordingly.
More edges are inserted via multi-cutting in order to extrude more faces. From there, the selected faces on the side of the ship are detached from the overall mesh, forming the docking bay door.
The model is moved upwards from the grid.
The faces formed earlier by multi-cutting are then extruded..
..and the top surface is then bevelled for smoothness.
19/5/20 (starting on the ship interior):
A cube primitive is inserted.
The cube primitive is then positioned inside the ship model, flattened and scaled to the width of the ship.
After being turned into a flat rectangle inside the ship model, the cube is extruded multiple times in order to match the shape of the ship, thus forming the ship floor.
This is then combined with the ship model via the combine tool and its vertices are merged with those that are part of the original ship mesh and also adjacent to the floor's vertices in order to seal the gaps properly.
20/5/20 (continuing work on the ship interior):
Edge loops are inserted on the other side of the ship.
An entire edge loop across the top of the front of the ship is created via the multi-cut tool.
The same is done for between the walls separating the windows.
Another edge loop is inserted around the top middle of the ship.
Faces on the insides of the walls of the ship are extruded in order to help form the interior walls separating the different rooms/sections of the ship.
24/5/20 (continuing working on the ship interior):
Faces on the front and back of each outer extrusion are deleted so that new, cleaner faces can be created.
The insides of the walls separating the docking bay, open space and sleeping quarters are covered up via extrusion and vertex merging.
The segment of the floor separating the areas mentioned above and the cargo bay is extruded upwards.
Vertices are then inserted along the edges of the walls via multi-cutting and merged with the cargo bay wall's vertices.
25/5/20 (continuing work on the ship interior):
Edges along the inside of the wall are deleted as part of cleanup.
The faces on the outside of the other walls are also deleted.
Edge of the floor of the hallway leading to the bridge is extruded.
Vertices are cut along the edge of this extrusion..
..and merged with those of the bottoms of the walls separating the rooms across the middle of the ship.
The process from earlier is then repeated with this face being extruded upwards..
26/5/20 (continuing work on the ship interior):
..and vertices being cut in the adjacent edges for merging in order to close gaps properly.
Once again, the edges created on the insides of the walls are deleted for cleanup.
More edges are inserted along the top of the windows via multi-cutting and edge loop insertion as a marker indicating where the extrusions for the walls separating the Captain's quarters, cockpit and break room will take place on the floor faces.
Using this indicator, the edges that are planned to be extruded are created via multi-cutting.
Multiple faces near the edge of this surface are extruded slightly upwards in order to properly form the cockpit.
Because of this, the vertices on the edge of the cockpit floor are merged with those on the window frames in order to maintain the ship's original shape.
27/5/20 (finishing work on the ship interior and starting on UVs):
A face on the cockpit floor within one of the window frames is extruded in order to fill it in..
..and its vertices are merged with the outside surfaces so that once again, the gaps are properly filled.
Due to being short for time, this process went unfinished. Thus, the edges and vertices created as guidelines are deleted for cleanup.
A planar UV map is created for each surface on the ship mesh.
The map is then unfolded until it is as flat as it can possibly be, thus greatly reducing texture distortion.
Additionally, if the surface loops around, one of the edges is cut so that the map can be unfolded properly.
28/5/20 (finishing the ship UVs, as well as the overall model):
Once all of the maps are created and unfolded, they are all neatly grouped together, selected and scaled down in order to fit in one big square on the grid.
The same process is then repeated for the docking bay door, which is a separate model. From here, the ship is now as complete as it could have gotten within the time frame and ready to be textured.
Team crisis management/contingency plan:
If a member of our team is absent, it will affect what can be completed and the stress of people gets increased because other people will take action over the work that the other members need to get completed. Jordan Page, the group leader, will be taking over anything that needs to be done that isn't currently being worked on between each role.
Harry Reader is our spokesperson, if he's unavailable then it's Jordan Page, then Bryant Haring, George Holt, then Harry Lewis.
Client is updated only if they need to be. When they come in they will be updated regardless if there's anything that we need their thoughts on or not.
In the event of the team having a crisis, details of the crisis itself are recorded on the team's Trello at https://trello.com/b/7xiGaeVs/team-2, and if the team doesn't check the Trello to see if there's a crisis then they are informed through other communication means e.g. text messages, calls, Discord direct messages, etc. The team will also be updated through these ways or other ways that they prefer to be contacted by.
29/4/20 Meeting:

In this meeting, we discussed what we've been working on and let each other know about our smart targets. We also decided on our agenda for the day (and to an extent, the days building up to May 6th.)
Members that participated:
George Holt
Bryant Haring
Harry Lewis
Harry Reader
Members that were absent:
Jordan Page
Agenda:
George - I will be doing smart target work and other blogger/trello work while waiting for concept art of the exterior of the ship so that I can adapt it into a
3D Maya model.
3D Maya model.
Bryant - Will be working on concept art.
Harry R - Will work on music for the levels.
Harry L - Currently deciding on what to work on.
Jordan - Unknown. However, Bryant has already filled him in on information given to us by Foxy.
6/5/20 Meeting:

Participants:
George
Bryant
George
Bryant
Absent:
Jordan
Harry L
Harry R
Jordan
Harry L
Harry R
We told each other what our goals are for the week and when we think they'll be done by.
13/5/20 Meeting:
Meeting Participants:
Harry Lewis
Harry Reader
George Holt
Bryant Haring
Members who were absent:
Jordan Page
Jordan Page
We discussed progress on the coding, multiplayer will be an addition to the game now. More level assets have been created. The level's exterior is nearly completed and the interior will be completed soon (most likely by next week).
Development Log
Keypad Model
24/3/20 (continuation of working on the keypad model):
Extruded the faces near the top of the keypad to start forming the anti-glare hood.
Dragged the vertices on the bottom edges of the hood and merged them with the surface vertices.
Angled the top of the hood.
Inserted an edge loop on the back of the hood.
Dragged the edge loop outward to make the hood look more curved.
31/3/20 (completing the actual modelling process for the keypad):
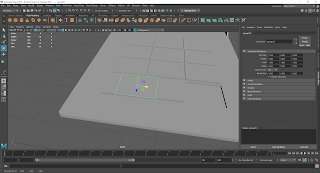
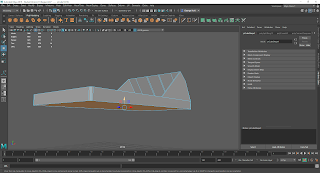
Dragged the bottom of the base downwards for extra thickness.
1/4/20 (UV-mapping the keypad and its buttons):
Created planar UV Maps for each for each surface on the mesh.
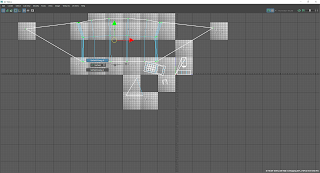
Unfolded each surface in the UV editor.
Shrunk the completed UVs into the first big square on the map for easier texture photoshopping.
Fully UV-mapped mesh.
The same UV-mapping process is done for each of the buttons.
The buttons are dragged back into place without being combined with the base mesh, and thus, ready for being animated.
Memory Chip Model
8/4/20 (modelling and UV-mapping the memory chip in its entirety):
A cube primitive is created.
The cube is then scaled up into a cuboid shape, forming the base of the chip.
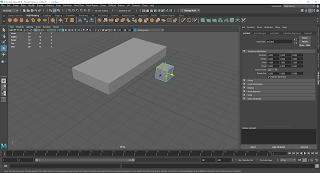
Another cube primitive is created.
The cube is then extruded.
Once extrusion is complete, the curves are bevelled in order to look smoother.
The mesh is then scaled appropriately, forming the prongs.
The edges of the base are bevelled.
The prong mesh is duplicated up to 32 times, so that 33 will be on either side.
The end of the base is dragged out to fit all 33 pairs of prongs.
Width of the base is also increased, but again, by dragging out one of the faces so that the first set of prongs stays in relatively the right place.
The prongs are mirrored in order to form the second set, which will be placed on the opposite side.
The two prong sets are then separated from each other for the time being.
A planar UV map is created for the faces on the base.
For any maps that loop around, a random edge on it is cut in order to ensure it unfolds properly.
The maps are then unfolded until they are neat enough so that distortion is reduced as much as possible.
The same process is then carried out for the UVs for the prongson the right...
... as well as the UVs for the prongs on the left, separately. Additionally, once the UV map for one of the prongs on one side are complete, the others on that side are deleted and replaced with new ones with the complete UVs via the aforementioned duplication process.
All the meshes are then combined with each other.
15/4/20 (finishing the memory chip UV):
After the meshes are combined, all the UVs in the combined object are then properly separated from each other, ready for texturing.
Control Panel Model
16/4/20 (starting on the control panel model):
Inserted a cube primitive.
Scaled up the cube into a more flat, rectangular shape to form the base of the panel.
Inserted edge loops all over the base for extrusion.
Extruded the faces that form the main screen frames.
Merged the vertices in the corners of the frame in order to make it more edged.
Used the connect tool to connect corner vertices and make the edges look more visible and polished.
Extruded the screen faces out a little bit to more easily separate them from the rest of the base.
Extruded the faces separating the three screens.
The vertices of the frame and the faces separating the screens are merged for additional clean-up.
More edge loops are inserted in order to extrude the faces representing the buttons.
The square faces on the base are extruded, forming the buttons.
The multi-cut tool is then used to create octagon-shaped faces in the base.
17/4/20 (continuing with the control panel):
Two of the vertices in each octagon face are properly connected once cutting is complete due to the cutting failing to register otherwise.
Excessive edges are then deleted and the octagon faces are extruded.
The front faces are then scaled down on all axes to form a more frustum-like shape and thus make them look more like dials.
Even more edge loops are inserted in order to create the faces that represent the sliders.
The faces representing the frame of the sliders are then extruded..
...followed by the faces representing the sliders themselves.
20/4/20 (finishing with the actual modelling process for the control panel):
Edge loops are inserted near the bottoms of the dials.
The new faces formed by this are then extruded to complete the dials by making them stick out from the base more.
22/4/20 (applying final cleanup and UV-mapping to the control panel):
Excessive vertices and edges are removed from the back of the base.
A planar UV is created for each surface on the mesh.
If the surface loops around, a random edge is cut in the UV editor in order to ensure the map is completely flat upon unfolding.
The map is then unfolded and all UV distortion on that respective surface is removed.
Additional edge/vertex cleanup is carried out on the slider frames.
Once all the surfaces on the control panel have been UV-mapped, they are then organised and grouped together and scaled down to fit into one big square on the graph. From there, the model is ready to be textured.
Ship Model (exterior)
6/5/20 (beginning work on the exterior of the ship model):
Inserted a sphere primitive.
Dragged out and scaled out parts of the circle in order to create a more spaceship-like shape.
Faces on the back of the mesh are deleted.
The hole is then filled back in with the fill tool...
Vertices on either side of the face are then joined together via the component connector tool in order to form new vertices, whilst still ensuring that the centre surface is flat.
The same face is then scaled and positioned to match the intended shape.
Vertices along the edge of the top surface are positioned in order to form a straight set of edges.
The top surface is then deleted and filled back in for flatness.
Excess vertices are then deleted as part of cleanup.
The mesh is then scaled up in order to match the intended proportions (so that it is in accordance to concept art).
11/5/20 (continuing with the ship exterior):
Circular edge loops are formed by vertices which are created with the multi-cut tool.
The circles formed from multi-cutting are then extruded.
The surfaces on the tops of the extruded circles are then deleted and re-filled.
These faces are then poked..
..and dragged out in order to make the surfaces look flatter and more organised when they are deleted again.
Once the surfaces are re-deleted, the edge loops on the ends of each cylinder are scaled outwards from each other in order to look more separated from each other.
Through the use of the edge loop insertion tool, edge loops are inserted on the front of the mesh.
The vertices on the top ends of both pairs of loops are joined together via the component connection tool.
The surfaces in between these inserted loops are then extruded inwards a little bit, thus forming the ship's windows.
With the windows extruded, the connections inserted earlier are deleted as part of clean-up.
Gaps in the edge loops are then joined together via vertex connecting.
12/5/20-13/5/20 (finishing the ship exterior):
The edge loops on the insides of the cylinders on the back are extruded inwards..
..and the vertices on the end of each edge are merged together so that the holes are properly filled in.
The centre vertices of certain surfaces are dragged into the edges and vertex merged into them.
Sometimes, these centre vertices are chambered via the vertex chamber tool before being merged in order to properly close the holes.
The edge loop on the bottom end the base of the ship is extruded in order to ensure that the sides of the ship are at 90-degree angles.
The edges on the ship's side inserted from earlier are then re-positioned accordingly.
More edges are inserted via multi-cutting in order to extrude more faces. From there, the selected faces on the side of the ship are detached from the overall mesh, forming the docking bay door.
The model is moved upwards from the grid.
The faces formed earlier by multi-cutting are then extruded..
..and the top surface is then bevelled for smoothness.
19/5/20 (starting on the ship interior):
A cube primitive is inserted.
The cube primitive is then positioned inside the ship model, flattened and scaled to the width of the ship.
After being turned into a flat rectangle inside the ship model, the cube is extruded multiple times in order to match the shape of the ship, thus forming the ship floor.
This is then combined with the ship model via the combine tool and its vertices are merged with those that are part of the original ship mesh and also adjacent to the floor's vertices in order to seal the gaps properly.
20/5/20 (continuing work on the ship interior):
An entire edge loop across the top of the front of the ship is created via the multi-cut tool.
The same is done for between the walls separating the windows.
Another edge loop is inserted around the top middle of the ship.
Faces on the insides of the walls of the ship are extruded in order to help form the interior walls separating the different rooms/sections of the ship.
24/5/20 (continuing working on the ship interior):
Faces on the front and back of each outer extrusion are deleted so that new, cleaner faces can be created.
The insides of the walls separating the docking bay, open space and sleeping quarters are covered up via extrusion and vertex merging.
The segment of the floor separating the areas mentioned above and the cargo bay is extruded upwards.
Vertices are then inserted along the edges of the walls via multi-cutting and merged with the cargo bay wall's vertices.
25/5/20 (continuing work on the ship interior):
Edges along the inside of the wall are deleted as part of cleanup.
The faces on the outside of the other walls are also deleted.
Edge of the floor of the hallway leading to the bridge is extruded.
Vertices are cut along the edge of this extrusion..
..and merged with those of the bottoms of the walls separating the rooms across the middle of the ship.
The process from earlier is then repeated with this face being extruded upwards..
26/5/20 (continuing work on the ship interior):
..and vertices being cut in the adjacent edges for merging in order to close gaps properly.
Once again, the edges created on the insides of the walls are deleted for cleanup.
More edges are inserted along the top of the windows via multi-cutting and edge loop insertion as a marker indicating where the extrusions for the walls separating the Captain's quarters, cockpit and break room will take place on the floor faces.
Using this indicator, the edges that are planned to be extruded are created via multi-cutting.
Multiple faces near the edge of this surface are extruded slightly upwards in order to properly form the cockpit.
27/5/20 (finishing work on the ship interior and starting on UVs):
A face on the cockpit floor within one of the window frames is extruded in order to fill it in..
..and its vertices are merged with the outside surfaces so that once again, the gaps are properly filled.
A planar UV map is created for each surface on the ship mesh.
The map is then unfolded until it is as flat as it can possibly be, thus greatly reducing texture distortion.
Additionally, if the surface loops around, one of the edges is cut so that the map can be unfolded properly.
28/5/20 (finishing the ship UVs, as well as the overall model):
Once all of the maps are created and unfolded, they are all neatly grouped together, selected and scaled down in order to fit in one big square on the grid.
The same process is then repeated for the docking bay door, which is a separate model. From here, the ship is now as complete as it could have gotten within the time frame and ready to be textured.
What is your team crisis management and details of agenda from today?
ReplyDeleteWhat is your role and show development in your role on this page. Screen grabs? Notes?